Gallery opened: Nov 2001
Updated: 6 Oct 2024
New Wikipedia link added here.
More on recent research at Southampton
The Short but Loud Story of Compressed-Air Amplification
"Have you heard the auxetophone? It is to be hoped not. All Mr. Parsons' turbines will be wanted to take long-suffering humanity out of earshot of his diabolical invention"
| 
| |
Before electronic amplification became practical, the volume obtainable from gramophones was strictly limited. Here are some early efforts to do something about it.
There is now a page on compressed-air gramophones in Wikipedia.
EDISON'S AEROPHONE: 1878.
Thomas Edison appears to have been the first to use a compressed air amplifier, both to overcome the problem of lack of replay volume for his phonographs, and to amplify the human voice. They appear in a British patent he took out in 1878. The idea of Short and Parsons did not emerge until twenty years later.
NB: In common usage an 'aerophone' is a musical instrument that produces sound mainly by causing a body of air to vibrate, without using of strings or membranes.
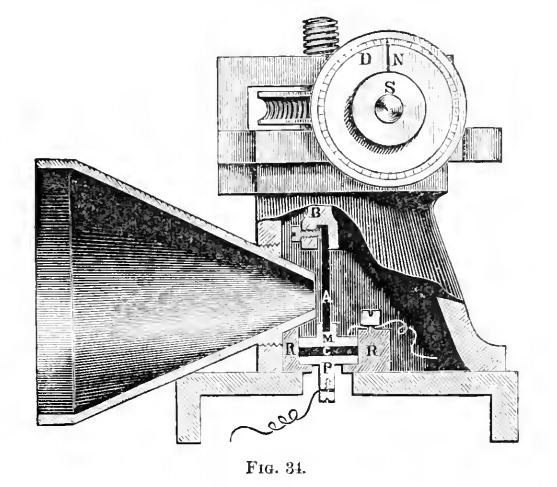 |
| Left: Not Edison's Aerophone: 1878
This image is frequently claimed to be the 'microphone' of the Aerophone. It is not. It is a tasimeter,
Bill Todd has pointed out to me that Popular Science Monthly seem to have used the wrong drawing. The same drawing was published in the American Journal of Science (Vol. s3-17, Issue 97, 1879) which describes it as a tasimeter, an instrument for measuring infra-red radiation devised by Thomas Edison. The 'mouthpiece' is a collecting horn for the radiation.
Source: Popular Science Monthly Volume 14, 1878 - 1879, p141
|
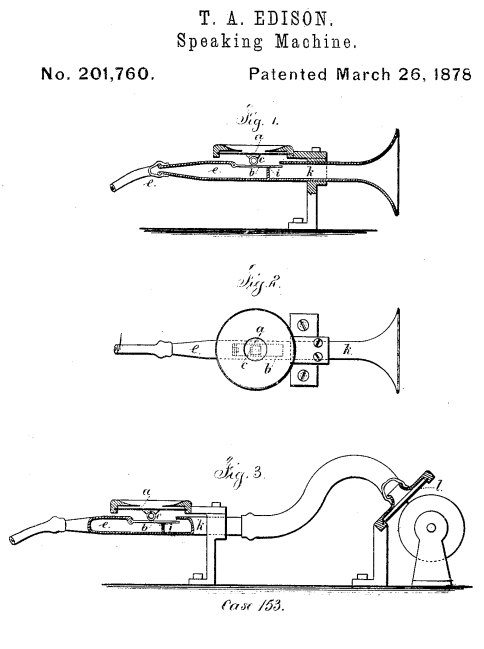 |
| Left: Edison's Aerophone patent: 1878
This appears to be the relevant Edison patent. In the upper drawing Fig 1 you speak into the horizontal diaphragm on top, and this is connected to a valve which modulates the flow of air coming in from the left. Although the title of the patent is 'Speaking Machine' it would presumably amplify any sound presented to it. In fact, you might have to careful about feedback, since the output horn is not very far from the input diaphragm. That would not sound nice.
Fig 2 is a plan view.
The lower drawing Fig 3 shows the Aerophone connected not to an output horn, but an output diaphragm which impresses the vibrations onto a stylus, which appears to be cutting a wax cylinder. Presumably the idea was that you record sounds to faint to operate a standard cutting machine.
Source: US patent 201,760 of March 1878
|
 |
| Left: Edison's Aerophone patent: 1878
This is an enlarged version of Fig 1 just above, giving a clearer view of how the diaphragm pressed on the air valve.
Source: US patent 201,760 of March 1878
|
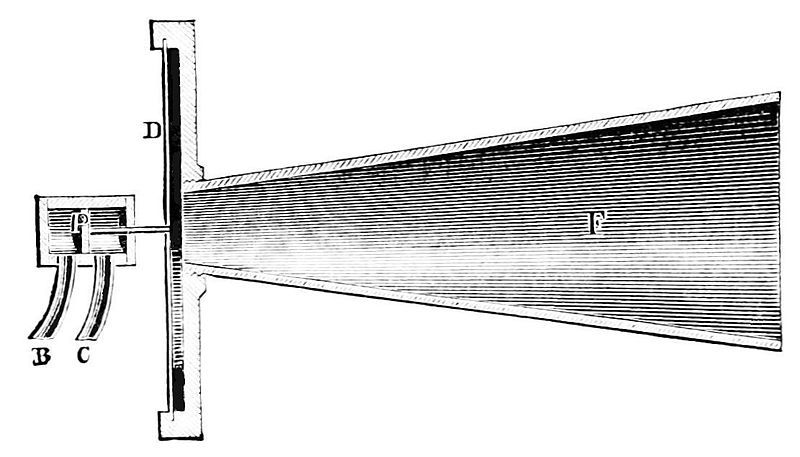 |
| Left: Edison's Aerophone: 1878
This is the business end of another version of the Aerophone. Here the modulated compressed air moves a piston in a double-acting cylinder, which actuates diaphragm D.
This is completely different from Short & Parson's Auxetophone, which applied the modulated air directly to the apex of a horn.
Source: Popular Science Monthly Volume 14, 1878 - 1879, p141
|
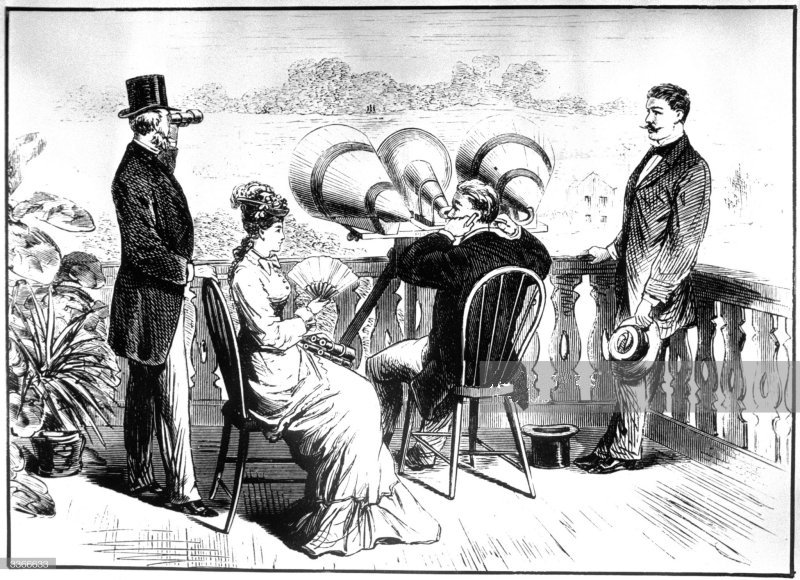 |
| Left: Not Edison's Aerophone: 1878
This drawing is often reproduced as showing the Aerophone being used for two-way communication. The transmitting horn is in the middle and either side are two receiving horns arranged for binaural operation. It probably would have been advisable to take the receiving ear-pieces out before transmitting. The party is presumably communicating with the three dark figures seen in the distance.
However, I am not convinced. There is no sign of a compressed air supply. Close examination of the transmitting horn shows that it has a mouthpiece at the narrow end. This is just a trial of a megaphone combined with listening horns as used in sound-locators. It was known as‘Edison’s Telephonoscope’ which he tried to promote early in 1878. The public were not impressed with a communication sytem that could only work on line-of-sight and was about as insecure as any system could be.
Historical note: the lady is carrying binoculars that are long compared with modern versions; this was before the invention (or popularisation) of prismatic binoculars.
Unknown artist
|
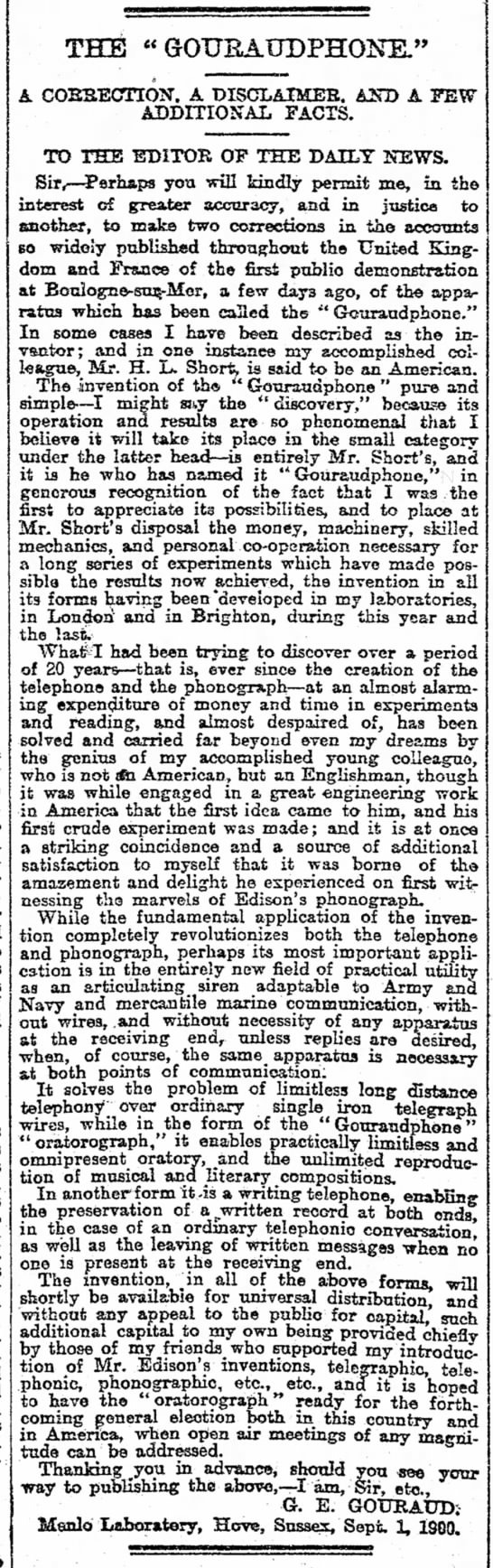 |
| Left: The Gouraudphone in an English newspaper: 1900
An collaborator with Edison in the promotion of the phonograph, the American George Gouraud met Horace Short in 1898, (he was the youngest of the three Short Brothers of later aviation fame) and for two years financed Short's researches into compressed-air amplification in the seaside town of Hove in Sussex, England. He produced a system that improved on Edison's Aerophone, presumably by the elimination of the piston-and-diaphragm transmittting arrangement. This was named the Gouraudphone and demonstrated at the Paris World Exposition in 1900.
I like the way the instrument is described as a 'articulating siren'. Presumably the idea was to shout across the battlefield- using code-words I imagine.
Source: Daily News, England, 4th Sep 1900, Tuesday. P8
|
THE AUXETOPHONE: 1898-1918.
Two Englishmen, Horace Short and Sir Charles A Parsons (yes, the steam turbine man) introduced the compressed air amplifiers known as Auxetophones. Horace Short began the development of the idea and was granted a patent in 1898, and again in 1901. The patent rights were sold to Parsons in 1903. Parsons, who was noted for his skill as a craftsman, took on the development of the Auxetophone as a hobby when he was already financially secure from his steam turbine business, and applied it to musical instruments as well as gramophones.
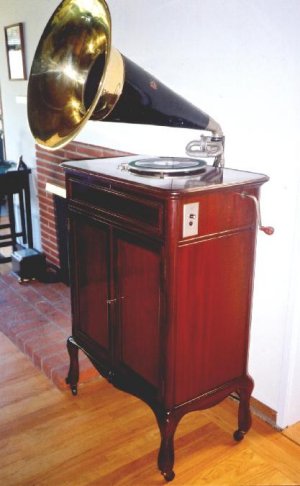 |
| Left: The dreaded Auxetophone ready to open fire on a defenceless audience.
This is a Victor machine, owned by Rene Rondeau.
The heart of the Auxetophone, housed in the "Parsons-Short soundbox" at the end of the tone arm, was the air-control valve. This was a sort of grid-iron valve consisting of a metal comb rigidly connected to the needle carrier, which opened and closed fine slots in the valve seating. The resulting pulsations of compressed air were passed to the horn.
Air pressure was provided by a 1/6 horsepower electric motor, and particles were removed from the air by what appears to have been a sort of oil-bath filter, as once used on cars. Clearly the aierophone
rol valve would have been susceptible to dirt and fluff.
One of the problems seems to have been the absence of any kind of volume control; probably some sort of air-pressure regulator would have worked. No technical details seem to be available on its distortion performance, but from the comment above it was probably pretty bad.
Note that although electric power drives the compressor, the turntable motor is still a clockwork three-spring motor wound by hand, which seems rather strange. Perhaps some sort of electrical remontoire (rewinder) for the driving spring would have worked? The small silver plate near the crank-handle is the on/off switch for the compressor.
You can now hear an Auxetophone for yourself; Rene Rondeau has put a video on Youtube.
Go to http://www.youtube.com/user/ReneRondeau (external link) and select the Victor Auxetophone video.
The distortion, while bad, is not as awful as I had been led to believe by the various comments made on it. What is noticeable is a loud background hiss of compressed air.
The volume also does not seem as devastating as claimed, but this is hard to judge as the recording equipment used to make the video probably had some sort of automatic level control.
|
HORACE SHORT
Horace Short was one of the brothers who founded the Short aeroplane manufacture business, which still exists in Belfast. See http://www.ctie.monash.edu.au/hargrave/short.html (external link)
Short was granted British Patent No 22,768 (granted 23rd September 1899)covering his development of the Auxetophone.
I have found a brief reference that says: "1898: The compressed air Auxetophone is first used to broadcast records of operatic arias from the tops of the Blackpool Tower in England and the Eiffel Tower in France." This was one Short's first prototypes; it gives you an idea of just how loud this thing could be.
A Short Auxetophone was heard all over Paris during the 1900 Paris Exposition, when it bellowed out Edison phonograph recordings from the top of the Eiffel Tower.
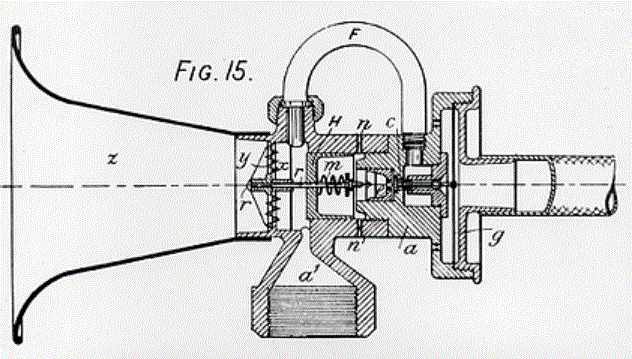 |
| Left: One of Short's patents
To my shame I have lost track of which patent this diagram comes from.
What we appear to have here is a two-stage control valve. The sound to be amplified comes in at the right, and the compressed air enters at the bottom through a'. The first-stage valve is in the housing a, operated by diaphragm g, and fed air through pipe f. The controlled air passes through the centre of the assembly to a second-stage valve at x. The holes n presumably vent excess air from the first valve.
|
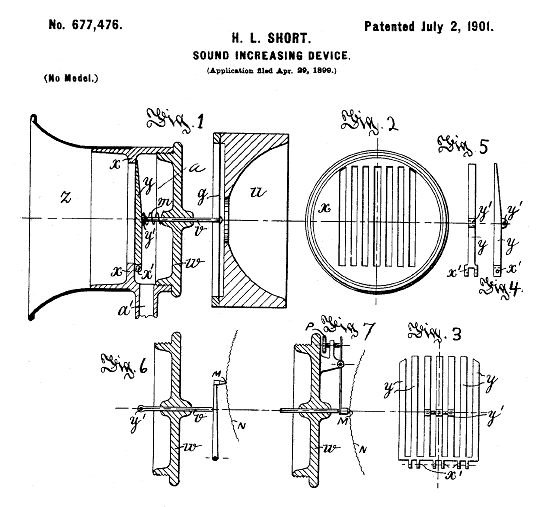 |
| Left: One of Short's patents: 1901
This version of the air valve appears to have a grid-type valve y hinged at the bottom that approaches and recedes from a series of slots to control the air supply, which enters at a'.
Fig 1 shows a voice-amplification system, with a microphone-type diaphragm at the right, which moves the valve via rod v.
Fig 6 appears to show a cylinder-phonograph version, with stylus m contacting the cylinder.
Source: US patent 677,476 July 1901
|
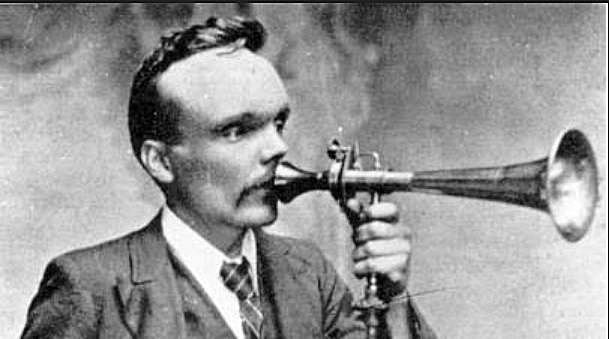 |
| Left: Horace Short holding the valve assembly of an auxetophone: date unkown
Assuming the compressed-air line is attached, he seems to be using it as a loudhailer.
Photograph courtesy of of Spirit Aerosystems.
|
CHARLES PARSONS.
In 1903 Short sold the patent rights to Parsons, and that year another British patent (No 10468) was granted, following Sir Charles' improvements to the air valve, the critical part of the system. In a letter written in 1921 to Sir Ambrose Fleming (The inventor of the thermionic diode valve) Parsons says:
"I worked at this subject as a hobby in my workshop at home and tried many types of valve- double-beat, slide-valves with multiple openings, then a form of valve made of sheet metal on edge like a fireworks cracker, and lastly the "comb-valve"- much the best because it delivered a flat-faced sound wave into the trumpet and it is not liable to be impeded or struck by small particles of dirt. It is similar to Short's. I made valves of comb pitches from 1/50 of an inch for reproducing from faint phonograph records, up to some of 1/4 inch pitch for attachment to double-bass stringed instruments. The very fine ones were made of hard gold, the rest of magnalium.* The air-valve reproducer was shown at the Royal Society about 1904, on a gramophone. Professor Johnston Stoney, FRS, was much interested, suggested the name "Auxetophone", and treated the matter mathematically.
If the motion of the valve is expressed in a series of sine terms (Fourier) the the sound wave produced is the first differential, and consequently the harmonics are much increased in amplitude above the fundamental, and the tone much increased in richness. This was found to be the case when used on the gramophone or when actuated from the bridge of a stringed instrument.
It was shown soon afterwards in the Library of the Royal Institution and notices appeared in the papers, and then Short's letter reached me. Previously I had not made any patent search and was not aware of his patent. Edison's had either been cited by the Patent Office or Marks and Clerk had known of it.
It appeared that Short had played an instrument on the top of the Eiffel Tower some years before. He (Short) was at that time connected with Colonel Gouroagh of the Edison Company, but when I met him he had very little money and readily assented to sell his patent to me for £700 down, and an agreement for four years at £400 per annum. Soon afterwards, the Gramophone Company of 21 City Road bought mine and Short's rights for gramophones and phonographs for all countries for £5000. I retained the rights for musical instruments.
The valve you have (taken to pieces) was made by Short in our Shops (at Heaton) and was played on a double-bass at the Promenade Concerts at Queen's Hall all one winter about 1906.
We spent much time and money in endeavours to introduce it on violins, 'cellos, and double-bass instruments, but were virtually blocked or boycotted by the Musical Fraternity, because they found it would reduce the number of executants from one-fifth to one-tenth for the same volume of sound. I dropped the whole matter, and Short was employed on other work including experimental attempts to make diamonds. He left our service about 1914 to join his brothers making sea-planes, and he died in about 1917, leaving £70,000, having made large profits from the Short Folding Wing Sea Plane.
The limiting factor to greater magnification of sound by means of an air-valve seemed to be viscous resistance in passing through minute apertures. Experiments showed that this was very marked below 1/1000 inch aperture. Hence there results a limit to the fineness of the comb. I was never able to obtain an actual magnification of the voice by means of an air-valve, Your (Fleming's) ionic valve has solved this problem."
* An alloy of aluminium and magnesium.
This letter appears to indicate that Parsons was interested in compressed-air amplification and developed the comb-valve before he bought Short's patent, which shows a different kind of valve. Perhaps it was the patent on the general principle, rather than the details of the valve technology, which Parsons wished to acquire.
It also raises the question of whether Short's voice-amplifier actually worked; Parsons says he could not make one that worked. Note also that Parsons does not seem to appreciate that one amplified double-bass is not remotely the same thing as five basses playing in chorus. And one can hardly blame musicians for being unenthusiastic about an invention intended to put most of them out of work.
How exactly did the air-control valve work? Since sound consists of positive and negative pressure changes, you might imagine that while the machine was "quiescent" there was a steady flow of air which was increased for positive excursions and decreased for negative ones. If this was not the case- and this point currently remains obscure- then the sound waveform would have been half-wave rectified, which would explain the poor sound quality. The supply of air to both sides of the tonebox may be related to this, or it may be to do with balancing the valve to reduce the frictional forces on it.
Later versions of the air-valve introduced partial balancing so that the relatively small needle forces could better control the pressurised air. A spring-loaded piston powered by the air supply acted on a wire-spring lever attached to the valve cover.
Parsons' first experimental air-valves had combs made of boxwood, the slits being cut with a jeweller's saw. The air pressure used in early tests was 2 to 3 psi.
Despite Parsons' and Short's efforts, the subjective results were apparently still somewhat short of perfection. One reaction from an Edinburgh journal was:
"Have you heard the auxetophone? It is to be hoped not. All Mr. Parsons' turbines will be wanted to take long-suffering humanity out of earshot of his diabolical invention".
The following letter was sent on 18th May 1909 by Sir Henry Wood, who co-founded the Promenade concerts in 1895:
"Dear Mr Parsons,
I am making a new orchestral arrangement for next season's Promenade Concerts at Queen's Hall of Wagner's "Siegfried" and I particularly want to do the scene with the Dragon's voice.
On the stage, this is always sung into a very large megaphone, but in my arrangement I want to do it on a very big bass tuba. do you think it would be possible for me to utilise your auxetophone? Of course I have never heard a tuba reinforced by your splendid invention, but perhaps during June, when I shall be fairly free, you could arrange for me to bring my player down."
Unfortunately nothing came of this innovative proposal, for Sir Henry wrote in the following June:
"Very many thanks for your kind letter. I had hoped to be able to the Royal College on the day you suggested, but was prevented. I now find that a bass tuba played into an ordinary very large megaphone (which I am having made by Hawkes*) gives the desired effect. With kind regards and many thanks..."
* Who went on to become part of the famous musical company Boosey & Hawkes.
A Victor auxetophone-gramophone was demonstrated to the public in November 1906 at a Trade Exhibition at Earl's Court. Mr S H Sheard recalled that the correct operating pressure had not yet been determined:
"We used about six or seven pounds to the square inch, with the rather amusing result that those of the audience who took the front rows of chairs very quickly clapped their hands to their ears and made their way to the back of the building. It was subsequently found that a pressure of not more than two-and-a-half pounds to the square inch was adequate." Which if nothing else proves that varying the operating pressure was a viable way of altering the volume.
In 1922-23, when wireless broadcasting had become established, the long-neglected auxetophones were resurrected at Parsons' Heaton works by Mr A Q Carnegie, one of Parsons' colleagues. A gramophone-type valve was driven by a magnetic motor, producing a high-volume output at a time when the capabilities of electronic valve amplifiers were very limited. The idea was not however pursued, one reason being that the patents had expired and this would limit the profitability of future business. The loudspeaker was still in use at the Heaton works in 1933.
Parsons took out three patents in all:
No. 10,468 (1903) Improvements in Sound Reproducers or Intensifiers applicable to Phonographs, Gramophones, Telephones and the like.
No. 10,469 (1903) Improvements in and relating to musical instruments.
No. 10,892 (1904) Improvements in and relating to Reproducers or Resonators for Gramophones, Phonographs and the like.
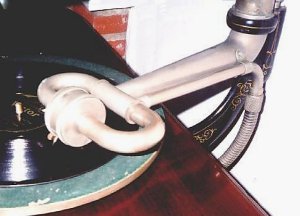 |
| Left: Close-up of the Victor machine pictured above, showing the tonearm, carrying the air-control valve.
One wonders about the sideforces on the needle generated by that armoured compressed-air pipe.
Note that air is fed to both sides of the valve box. |
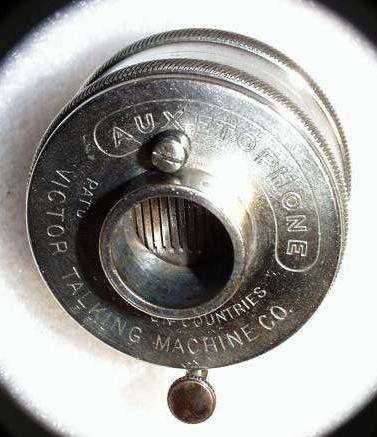 |
| Left: A close-up of the Victor valve box, showing the air-control comb valve. The thumbscrew at the bottom is to secure the gramophone needle. The screw at the top presumably adjusts the air valve.
The valve itself consisted of a pair of combs fitted tightly together. When quiescent, the two combs overlapped their teeth to form a seal, stopping the flow of air. When the needle bar moved, it slid one comb sideways, opened the spaces between the teeth and allowed air to flow.
Air was supplied to the input side of the combs, but some of the pressurized air was also fed to the horn (or output) side. The force holding the comb valve down when the groove of the record had not moved the needlebar was supplied by the slight overpressure on the horn side.
|
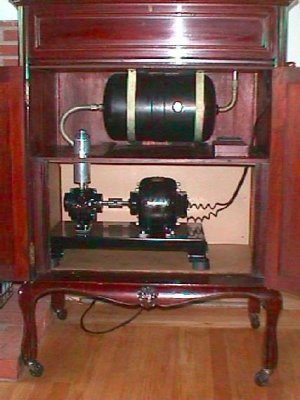 |
| Left: Inside the Victor.
The electric motor in the centre drives a small rotary-vane compressor, which feeds the sizable black air reservoir above, via the silver cylinder which is an oil separator.
No cutout switch to prevent over-pressurisation is visible, but it might have been housed in the plinth at the top, where the motor wires appear to go. One hopes there was at least a safety-valve. The working pressure was only 2.5 psi.
Note rubber mountings for the motor-compressor assembly.
This machine is owned by Rene Rondeau.
|
 |
| Left: The compressor of the Victor Auxetophone seen at the top of this page.
The compressor is at the left and the electric motor is on the right. Two nickel wick-type oilers can be seen just below the shaft bearing on the right of the compressor casing. These oilers have cotton wicks that stick up and contact the shaft; they are kept filled with light machine oil.
Photograph by kind permission of The Montana Phonograph Co.
More photographs of this Auxetophone can be seen at:
http://www.montanaphonograph.com/gallery/Auxetophone.html
|
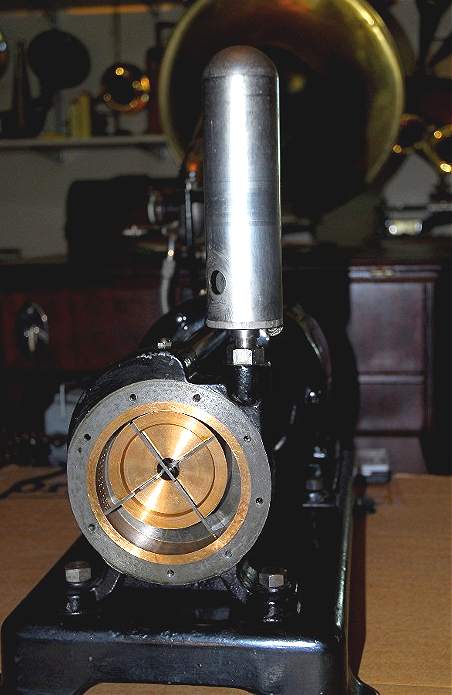 |
| Left: The compressor of the Victor Auxetophone seen at the top of this page.
The end of the compressor has been removed to show the rotating-vane principle of operation. The brass wheel turns anticlockwise, and air is drawn in by the sliding vanes through the numerous small holes on the left of the compressor casing, and pushed out through similar holes (not visible) on the right, and into the nickel-plated vertical cylinder, which is an oil separator. The operating speed is 1100 rpm.
Photograph by kind permission of The Montana Phonograph Co.
|
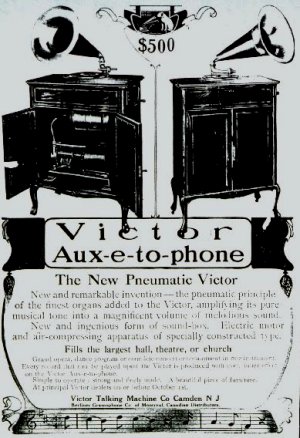 |
| Left: The Auxetophone was manufactured by Victor from 1906 ("the New Pneumatic Victor") until 1918.
Despite this long production run few were made. One reason was the price. £100 in 1906 was a year's wages for a clerk. The machine was not suitable for home use- but then it was not intended to be. The sound volume was reported as "extremely loud " and would have deafened the average home listener, not to mention his neighbours.
Auxetophone sales literature promoted its use in "large residences" but the real market appears to have been restricted to open-air cafes in parks and similar, despite the need for an electricity supply. Dance halls, theaters, and restaurants typically hired small or large bands, and there is not much doubt that their music sounded much better.
|
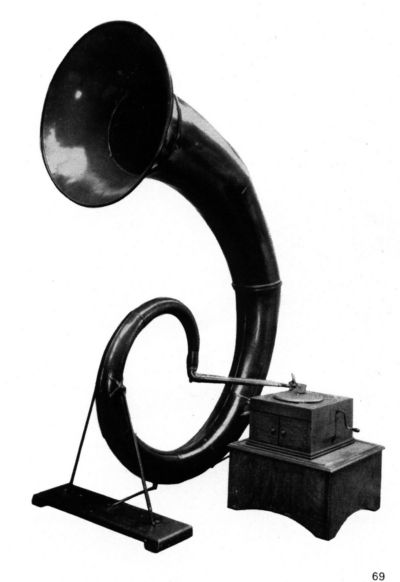 |
| Left: This appears to be an early model Auxetophone, possibly a prototype.
A Subjective Evaluation of The Auxetophone:
The following listening report was kindly provided by Dan Gilmore:
"I have heard a functioning Auxetophone and the only way to describe it is to liken it to standing in front of an air-raid siren, or a firing squad (LOL!). They are loud. Probably about 120+ db at about 3 feet from the horn. I'm guessing at the output volume because it was beyond the threshold of pain at about 10 feet.
The sound quality is fairly good provided you are about 50 feet away. It sounds like the music has undergone pulse code modulation. It's a very harsh sounding phonograph unless you are at a substantial distance away from it. I would think that any frequency beyond about 2000 Hz and below about 500 Hz are stripped out by the process judging from the way it sounded. A good approximation of how an Auxetophone sounded would be like listening to the record played through a bullhorn. Very flat sounding, but loud. I can see why previous owners modified them to use an Exhibition sound box.
120 or so dB is indeed loud! If you put a dB meter (unweighted sensitivity) in front of a Victor with an Exhibition soundbox at about 3 feet from the horn, and use a loud tone steel needle, acoustic era recordings will punch out as much as 85-90 dB. Edison Diamond Disc phonographs can punch out a whopping 95-100 dB. An Auxetophone at the 'threshold of pain' packs energy like a locomotive."
|
I understand that a picture of the auxetophone connected to a cello during the performance of a concerto with full orchestra is shown in the C A Parsons Co. Heaton Works Journal for December 1934. (Volume 1, No 6) I have no idea what an Auxetophoned cello sounded like; we can only be confident that it was LOUD.
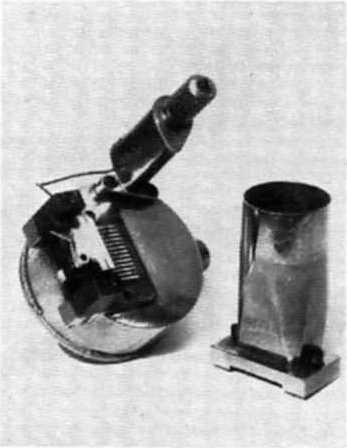 |
| Left: Early model of the Auxetophone valve for gramophone use.
|
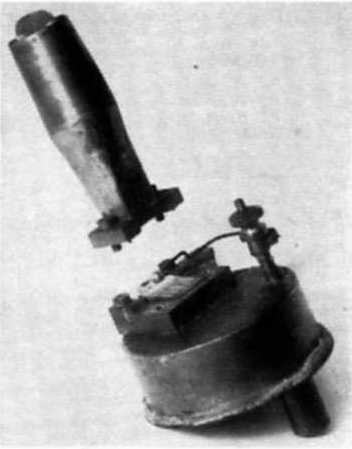 |
| Left: Standard model Auxetophone with upper part removed to show the valve grating.
|
 |
| Left: A double-bass fitted with an Auxetophone.
Presumably there is a flexible connection between the air-valve on the double-bass and the fixed horn. Note the pressure gauge laying on the floor at bottom left. This appears to be the same horn shown connected to a gramophone in the picture above.
Note: Appleyard's biography of Parsons states positively the instrument is a cello, but I have been told that, from the shape of the shoulders, this picture actually shows a double-bass. The horn must therefore be very large.
|
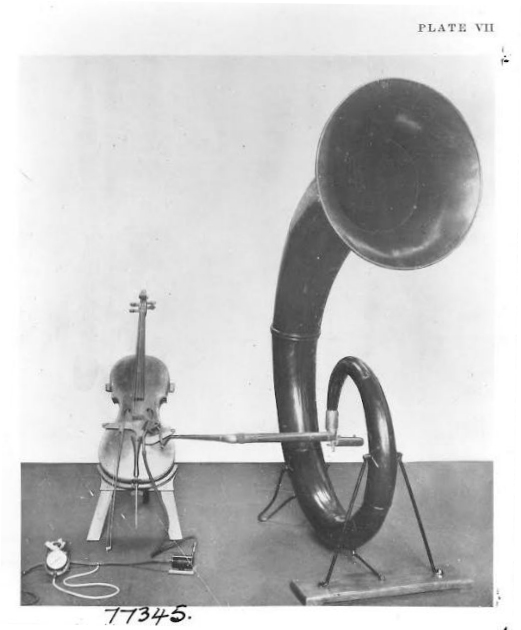 |
| Left: A cello fitted with an Auxetophone.
This actually is a cello, connected to the horn. Almost certainly taken at the same time as the double-bass picture above; note the same pressure gauge, and the same small black box between the gauge and the cello, which was probably some sort of pressure regulator.
Photograph courtesy of of Spirit Aerosystems.
|
I received the following message from Mr Ted Bowman in December 2013:
"In the 1920's my late father constructed a loud-hailer for use at Woolsington airport (now Newcastle airport) which enabled voice communication from the ground to pilots flying overhead. This consisted of a Parsons Auxetophone in which the air valve was actuated by a "reed" earphone. At that time my father earned his living building custom-made radio receivers for wealthy Northumbrians."
On a website devoted to the London tube system, there is said: "More than one attempt has been made to encourage considerate behaviour on escalators; an attempt was made, for example, in 1920 using a kind of compressed air amplifier that took a signal from a gramophone recording to bawl out 'Stand on the Right'. I have not so far been able to find out any more about this.
Bibliography: "Charles Parsons: His Life and Work" by Rollo Appleyard. Constable & Co Ltd, 1933.
OTHER APPLICATIONS: 1903
In 1903 in Germany Oscar Messter patented his new Auxtephone system which used compressed air amplifiers to feed special loudspeakers. No more details known at present.
THE PATHE GRAMOPHONE: 1907
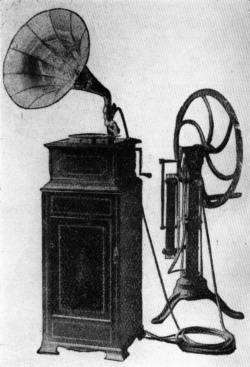 |
| Left: Pathe compressed-air gramophone.
This model has a hand-operated compressor. The length of the hose seems to indicate that the unlucky pump operator could be tucked away well out of sight and sound while the party went on.
|
COMPRESSED AIR IN THE CINEMA: 1907
George Kemp recalls:
"We had talking pictures in 1907. The film was run through the machine and it had a gramophone with it. The sound was amplified by compressed air. You had a blower which went into one of those trumpet things and the idea was to get the film and the gramophone to synchronise with each other, which wasn't always easy."
|
Clearly that was some sort of auxetophone, with an electric compressor.
Source: Pictures Past by Janet McBain. Moorfoot Publishing, Edinburgh 1985.
Twenty years before the ‘talkies’, the Panopticon advertised a variety of sound-film devices. First came Gaumont’s chronophone, which A E Pickard claimed was shown in Glasgow a day before London. A couple of years later, the theatre acquired another version of this technology, the auxetophone – so for a month or so in 1908, the Panopticon programmes included silent films on the bioscope as well as song films in the other two systems.
The very first valve amplifiers did not appear until 1906.
THE FORTOPHON STARKTONMASCHINE: 1908?
 |
| Left: The Fortophon Starktonmaschine.
This German machine pays very close homage to the Victor design; it may have been made under licence or may have been straight plagarism. Note that the electrically-driven compressor is definitely a rotary model.
"Starkton" discs were cut with wider groove modulation to produce high volume. Despite the suggestive name they were not produced by Stark Industries.
|
THE NATHANIEL BALDWIN MULTIPHONE: 1910
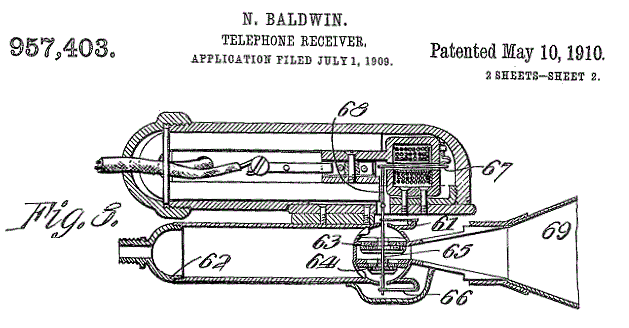 |
| Left: The Nathaniel Baldwin Multiphone: 1910
This compressed-air loudspeaker comprises a single diagram in US Patent 957,403, which deals mainly with earphone receivers. Presumably it was inserted there to save money on patenting.
Why it was called a Multiphone is unclear- perhaps because you could address a lot of people at the same time?
What appears to be an ordinary magnetic earphone receiver controls the two valves 63 and 64 via the rod 68. The top valve is larger than the lower so there is a 'quiescent currenr' of air flowing all the time, which is increased or decreased by movement of the valves. The compressed air comes in at the left and the sound then comes out of the horn to the right. According to a contemporary newspaper article: "Spoken words have been clearly heard a mile away"
Source: US Patent 957,403 of May 1910. This is the last Baldwin compressed-air patent found so far.
|
There is no sign that the Multiphone was developed further. There was nothing very novel about it.
There is some info on Nathaniel Baldwin on his Wikipedia page.
There is much more information here. Baldwin was a Mormon, (LDS) who came to be at odds with their leadership when he continued to argue for polygamous marriage when the LDS had (officially) abandoned it. Despite this, he only married once. He attended a conference of the LDS, and was struck by how hard it was to hear speakers in distant parts of the Salt Lake Tabernacle. As he later said: "...until that day nothing was further from my mind than the problem of amplifying sound. But, after that day, the thought could not be pushed into the background." At the time he was working as an electrician and air compressor operator at the Mountain Lake mine; compressed air was to hand.
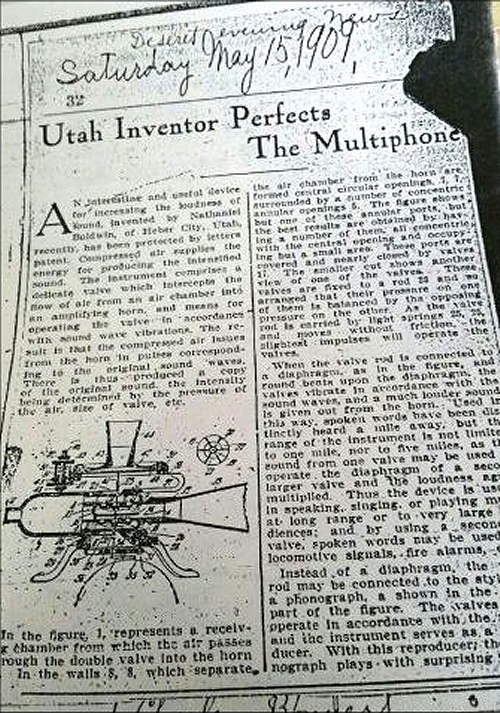 |
| Left: The Nathaniel Baldwin Multiphone: 1909
News cutting about Nathaniel Baldwin and his Multiphone. The version shown in the diagram comes from an earlier patent US 869,288 of Oct 1907. Voice input was via the horn on top; it could also reproduce phonograph cylinders, represented by the cylinder at the bottom.
Source: The Deseret Evening News, Saturday, 15 May 1909. The title comes from Deseret, a propsed Mormon state that was never recognized by the United States government.
Thanks to Steve Bringhurst for bringing Nathaniel Baldwin and his Multiphone to my attention.
|
 |
| Left: The Nathaniel Baldwin Multiphone: 1909
This is an earlier version of the Multiphone from the 1907 patent, which was reproduced in the news cutting above. Voice input was via the horn on top; it could also reproduce phonograph cylinders, represented by the stylus resting on the cylinder at the bottom of the diagram.
At first it looks as if you could do both at once (DJ in the house!) but I would have thought that speaking into the top horn would upset the tracking of the phonograph stylus. Another issue is that the amplifier, horn, and air hoses all had to be dragged sideways by the phonograph stylus as the cylinder played, which doesn't sound too practical to me.
Source: US Patent 869,288 of Oct 1907
|
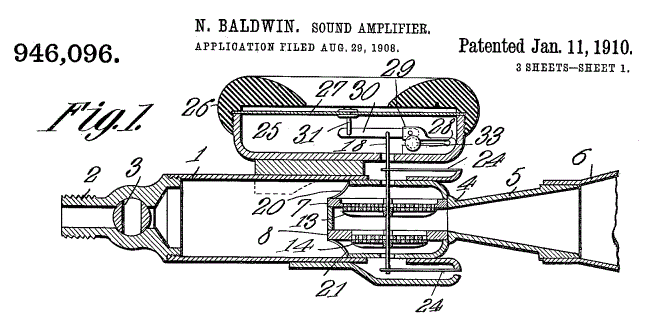 |
| Left: The Nathaniel Baldwin Multiphone: 1910
This looks like a development of the 1907 patent, with a different form of valve, and the phonograph facility dropped. The text of the patent is rather vague about how the valve actually works.
Source: US Patent 946,096 of Jan 1910.
|
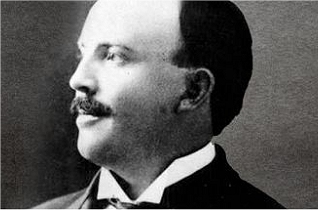 |
| Left: Nathaniel Baldwin: date unknown
Baldwin had a complicated life, that included a couple of years in prison for selling stocks by mail fraud. He carried on taking out patents for electromechanical loudspeakers into the twenties. He died in 1961.
Source: unknown
|
THE STENTORPHONE: 1910-21
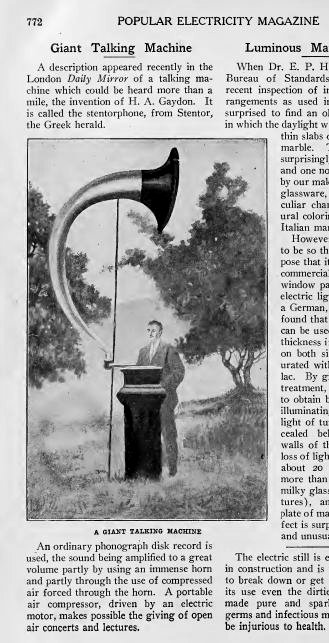 |
| Left: The Gaydon Stentorphone: 1912
This is the first reference to the Stentorphone found so far. Why the Stentorphone has been set up in an orchard, where electric power is not likely to be available, is currently not clear.
Source: Popular Electricity, Dec 1912
|
 |
| Left: The Gaydon Stentorphone:1914
The Stentorphone was produced by H A Gaydon. Stentor in Greek mythology, was a herald of the Greek forces during the Trojan War, and supposed to have had a particularly loud voice.
The Creed telegraph equipment company were active with the Stentorphone public address system in 1919-21. The valve power amplifier had not yet appeared and the Stentorphone allowed gramophone records to be amplified via a sound-box consisting of a comb-valve which sounds very much like Auxetophone technology. A number of Stentorphones were made and used at exhibitions, open-air concerts, and the like.
Obscure Fact: The name Stentorphone was used for an intercom system fitted to Cadillac cars around 1928, for communication with the chauffeur. How it worked is unknown- it was probably a simple voice-pipe.
|
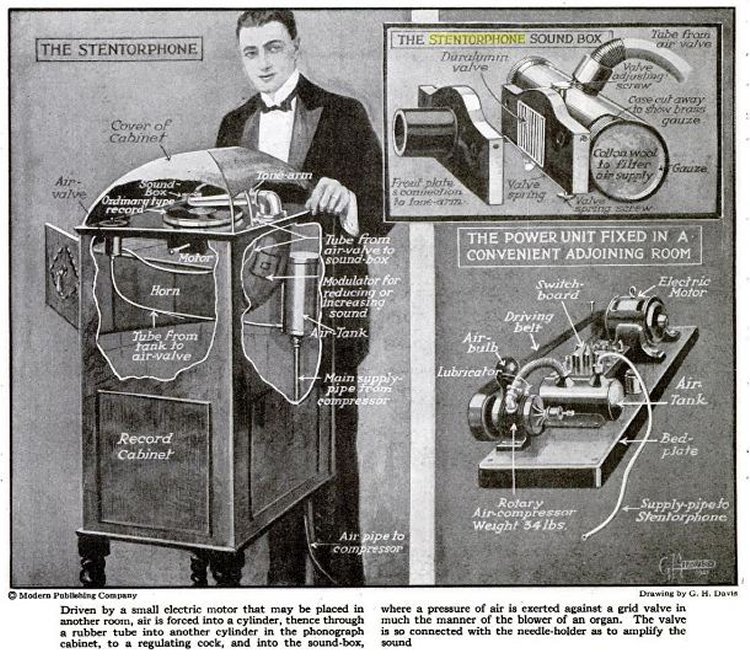 |
| Left: The Stentorphone in Popular Science: 1921
The brief article attached to this picture says nothing about who was manufacturing the Stentorphone at this point.
It is claimed in the picture that the air compressor alone weighs 54 pounds, which seems highly unlikely from the size of it; it is more likely the weight of the entire motor-compressor assembly. The 'air bulb' is mysterious; it looks too small to be of use as an air reservoir. In any case there is an 'air tank' to perform this function, in the lefthand picture.
Source: Popular Science Sept 1921
|
'Stentorphone' was also used as the name for a particularly loud pipe-organ stop.
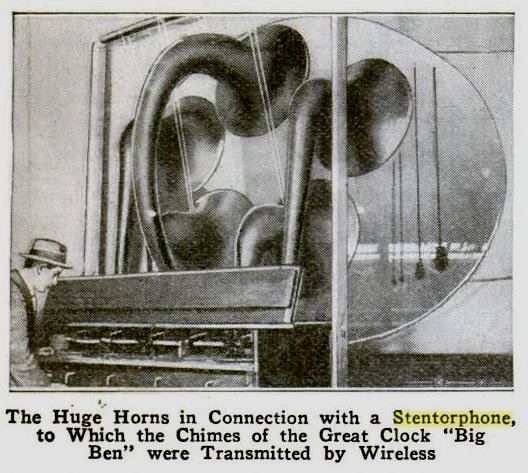 |
| Left: The Stentorphone in Popular Mechanics: 1921
This installation of five horns with associated auxetophone valves was use to reproduce the chimes of Big Ben at a London exhibition. Details are in short supply, but presumably the sounds of Big Ben were transmitted to the exhibition over telephone lines, and applied to coils driving the air valves.
This is the first mention found so far of a compressed-air loudspeaker controlled by an electrical input rather than a mechanical motion.
|
THE GAUMONT CHRONOPHONE SYSTEM: 1910
In 1903 French engineer Leon Gaumont was granted patents for loudspeaker systems to go with his sound on disc talking films, which used one of Berliner's Gramophones.
In 1910 Gaumont demonstrated his Chronophone system, which synchronised sound and film, at the Gaumont Palace in Paris. The compressed-air amplifier, whiuch he called the Eglephone, (LG being the initials of Léon Gaumont) was just a part of the whole system. The volume was enough for an audience of 4000. Initially the longest moving picture that could be made with synchronised sound was only 200ft, due to the limited playing time of the Gramophone record. (Projection was at 16 frames per second) Gaumont surmounted this problem by having two gramophone platters; a deft operator could switch between them to give a more or less continuous soundtrack.
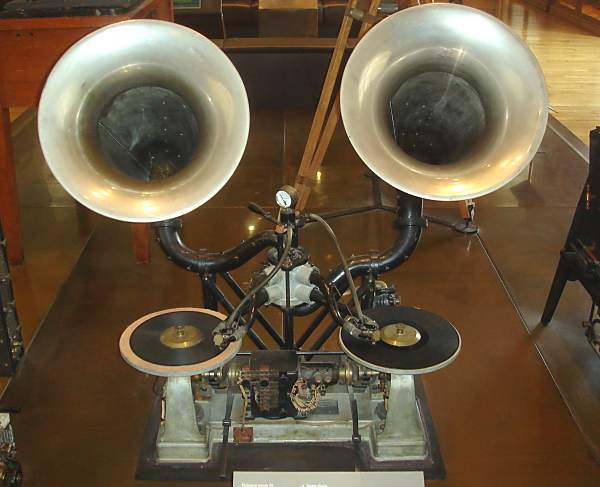 |
| Left: The Gaumont Chronophone: 1910.
Note the twin gramophones, driven from a common electric motor between them. An air hose goes to each valvebox from the control valve just under the air pressure gauge; I suspect that this control valve allowed the operator to crossfade between the two gramophones. DJ in the house!
Below this, there is a light-coloured metal manifold which connects the the gramophone output pipes to the two horns. Quite how the record arms are pivoted so they can follow the track on the disc is a bit unclear, but there appears to be some sort of ball joint where they enter the manifold.
The Chronophone now has a brief Wikipedia page.
Example in CNAM, the Conservatoire National des Arts et Metiers in Paris. Author's photograph.
|
 |
| Left: The Gaumont Chronophone: closeup of air valve and manifold. 1910.
For some reason that is so far quite obscure, the throat of each horn is studded with screw-heads.
Example in CNAM, the Conservatoire National des Arts et Metiers in Paris. Author's photograph.
|
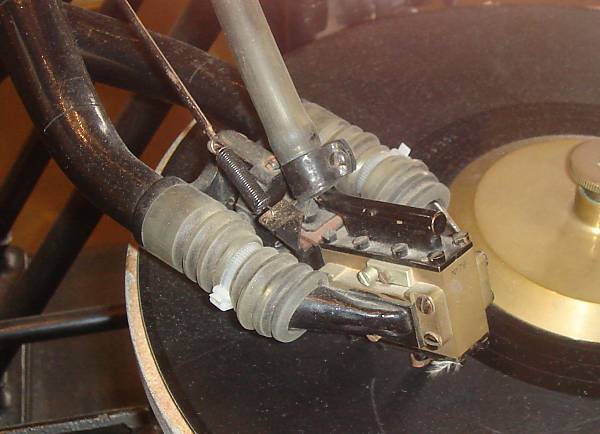 |
| Left: The Gaumont Chronophone: closeup of valvebox. 1910.
Compressed air enters the valvebox from above through the grey central pipe, and exits through the two pipes at each side. Note the diagonal wire and spring to reduced the otherwise enormous downward tracking force.
Example in CNAM, the Conservatoire National des Arts et Metiers in Paris. Author's photograph.
|
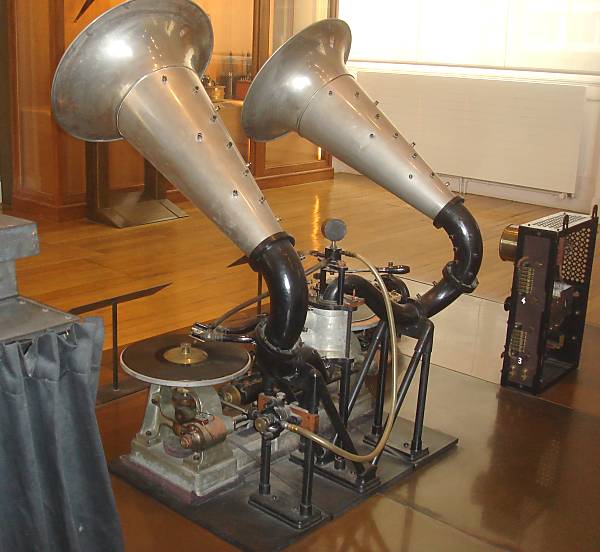 |
| Left: The Gaumont Chronophone: rear view. 1910.
From this angle it can be seen that the wider parts of the horns are also studded with mysterious screw-heads.
To the right is the electrical control panel of the system.
Example in CNAM, the Conservatoire National des Arts et Metiers in Paris. Author's photograph.
|
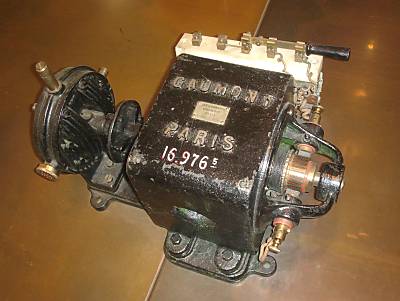 |
| Left: Electrically-driven air compressor for the Gaumont Chronophone
The brass label indicates that the motor ran off 110V. There is a rather dangerous-looking knife switch at the rear.
Example in CNAM, the Conservatoire National des Arts et Metiers in Paris. Author's photograph.
|
Gaumont was the first to suggest placing loudspeakers behind the screen, and carrying them about to follow the images on the screen! The human panpot was born.
PUBLIC ADDRESS IN GRANDVILLE
Grandville is a series of graphic novels by Bryan Talbot, depicting a steampunk world where the dominant species have animal heads and human bodies. Humans are very much second-class citizens. Inspector Lebrock is a badger, but also an inspector at Scotland Yard. On one occasion he was accused of badgering a witness. It's a brilliant series, rich in non-obvious allusions and references. If this webpage was the inspiration for Bryan's public address system, then I am a proud man.
Grandville is Paris. There's not much point in trying to assign a date, but the general feel of Grandville is Victorian.
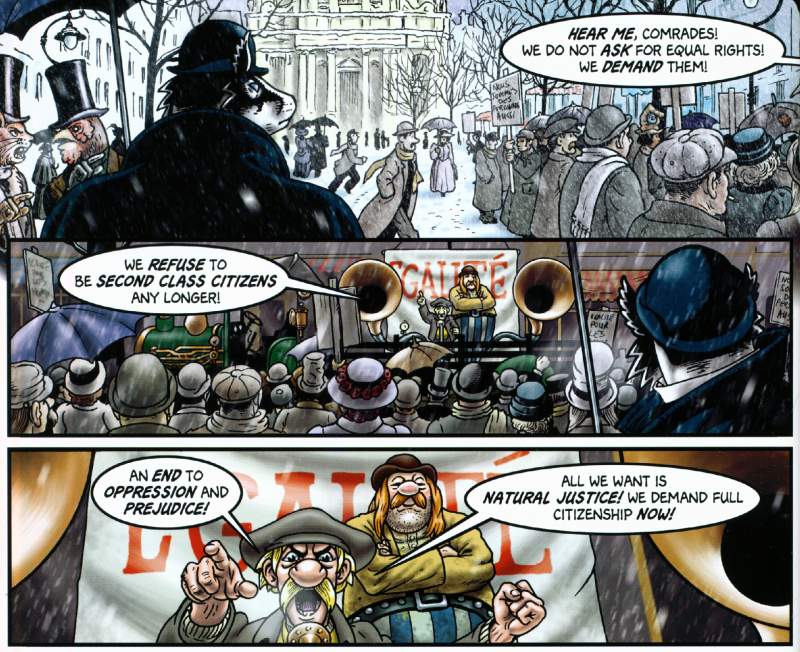 |
| Left: Asterix and Obelix address the crowd, while Inspector Lebrock looks on. Note the holes in his hat-brim for his ears.
Clearly based on the Gaumont Chronophone described just above. The pressure gauge clinches it.
Note that the PA is mounted on a trailer pulled by a steam traction engine on the left.
From Grandville: Noel, the fourth Inspector Lebrock graphic novel.
|
AUXETOPHONES IN AUSTRALIA: 1909
From The Evening Star (Western Australia) p3, 22 March 1909
"CHARITY CONCERT. A decided novelty was billed for Victoria Park last night, when the auxetophone, a mammoth gramophone, was at work, the accompaniments to the songs being played on the Themodist pianola. The effect was marred by the heavy wind blowing, but sufficient was shown to display the merit of the powerful song reproducer and with the accompaniments was most lifelike. Mr. M. D'O. Musgrove played the accompaniments. At intervals the band gave some choice selections, and the concert apart from weather conditions was most enjoyable, and should result in a fine addition to the funds of the league."
But what was a Themodist pianola? The Themodist feature allowed notes to be accented or subdued, if used with a pianola roll having appropriate encoding. For straight pianolas see here.
AUXETOPHONES IN AMERICA: 1911
Here are two quotes from The Talking Machine World for September, 1911:
"Mr Grimshaw is the patentee of trumpets. tone arms, etc., which are especially adapted for this kind of work. They are suitable for gramophones and auxetophones or for any disc talking machine. His taper tone arm is a perfectly straight one, having no bends or curves."
"Victor dealers will be interested in the report that J. Ed. Beach, of Springfield, Mo, is giving auxetophone concerts in the city park there and making a success of them. He pleases large crowds with his programs."
From The Talking Machine World for July 1911; Louis F Geissler, general manager of the Victor Company speaks at a convention:
"The remarkable Auxetophone was brought out by our company after an expenditure of nearly $75,000 in patents and developments- all this before one machine was marketed. It served and is still serving its purpose, and helped us on in development and' advertisement."
AUXETOPHONES IN CRICKET: 1921
This is from a report on the Headingley Test match in 1921.
"What made the day almost intolerable, however, was a gramophone, or rather a stentorphone, that bellowed advertisments at us during the waits. It asked us in a voice louder than was ever used for selling coal in the streets, 'Have you read the ---?' mentioning a paper of which you perhaps have never heard the name."
"At length the crowd could bear it no longer and groaned in impotent despair at each new mention of the paper. I foresee a time when all the rival papers will have stentorphones at cricket matches shouting racously against each other like bookmakers."
THE HETZEL COMPRESSED-AIR LOUDSPEAKER: 1929
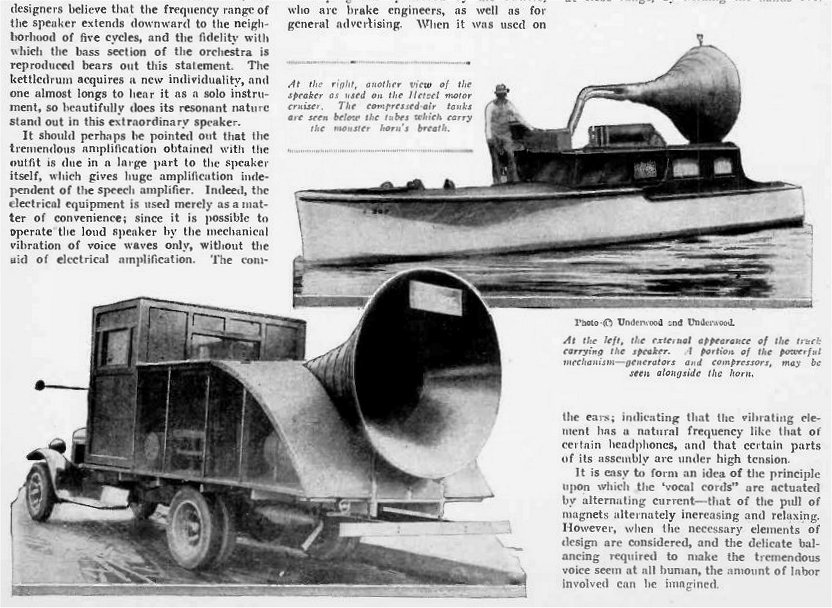 |
| Left: The Hetzel compressed-air loudspeaker: 1929
This huge public-address machine was built by the Hetzel Brothers of Los Angeles, at a cost of $16,000, for the purpose of publicizing their brake business. It was said to be audible four miles away.
The compressed-air was supplied by a compressor driven by a 60 HP petrol engine, independent of the truck's engine. This also drove a DC generator to provide a 1000 V anode voltage for two 50-Watt amplifier valves; these drove electric valves that controlled the air supply. There were four valves connected in parallel, for reasons that are not currently clear, and there were elaborate arrangements for using wet rather than dry air, for reasons that are equally obscure at present.
The loudspeaker was used both with microphone and phonograph record input. Both sources had to be housed in a sound-insulated box behind the driver's position, to prevent acoustic feedback.
Source: Radio-News for May 1929, pp986-987
Many thanks to Paul Reid for drawing this device to my attention.
|
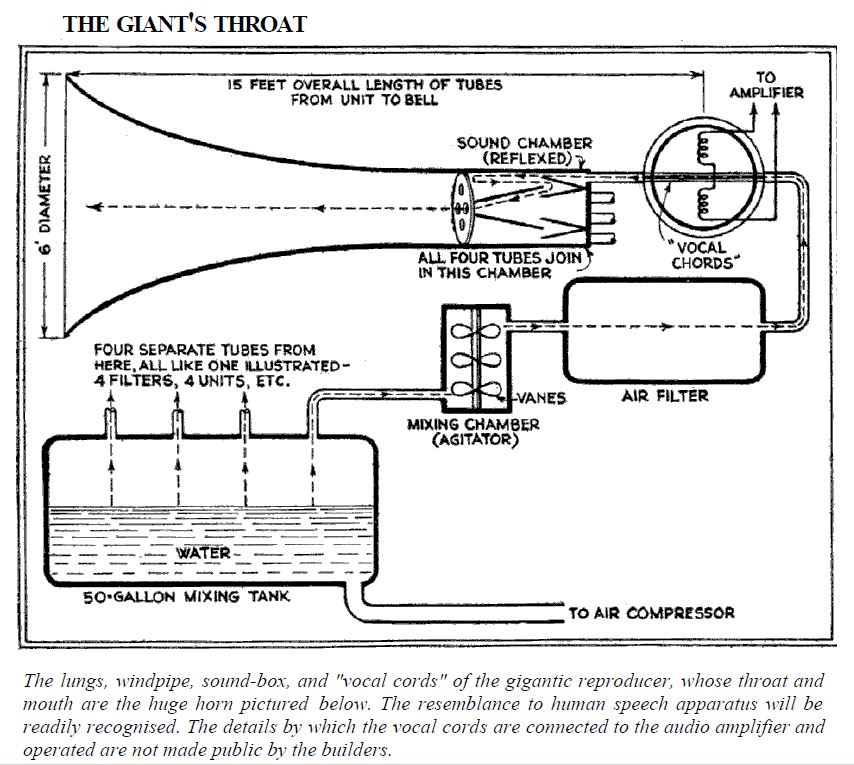 |
| Left: The Hetzel compressed-air loudspeaker: 1929
As noted above, the Hetzel loudspeaker used wet air for unknown reasons. This diagram shows how the compressed air was bubbled through a tank of water and then split into two halves. I assume the idea was that the air be saturated with water vapour rather than carrying a mist of droplets; the latter would have been removed by the air filter.
The author of the article made a a lot of the loudspeaker working like the human voice, the air valves corresponding to 'vocal cords' in that they impressed a pulsation on the air supply. The second vital feature of human speech is that this excitation waveform is then modified by several variable resonances, called formants. The Hetzel Hetzel loudspeaker did nothing like this- the modulated air supply was simply fed to a horn to match the impedance of the air.
In February 1933, US patent 1,898,302 'Pneumatic loudspeaker' was granted to Frank Hetzel. It describes a gate-type valve activated by an electromagnet. No mention is made of using fourfold paths or wet air.
Source: Radio-News for May 1929, pp986-987
|
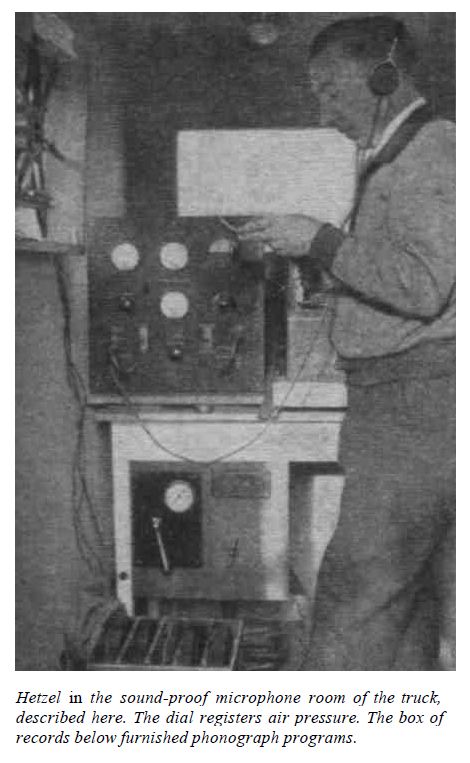 |
| Left: The Hetzel compressed-air loudspeaker: 1929
This is presumably Frank Hetzel, as he was the man who took out the patent. The black box with meters on the bench is presumably the amplifier with its 1000 V anode voltage.
Source: Radio-News for May 1929, pp986-987
|
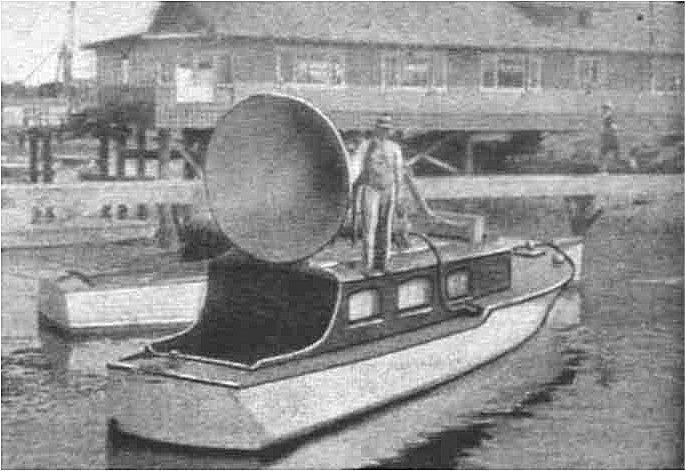 |
| Left: The Hetzel compressed-air loudspeaker: 1929
Here the Hetzel loudspeaker is mounted on a boat for the use of officials of the Newport Beach, California, Yacht club at a
regatta; the Hetzels were clearly good at finding opportunities for publicity. Speech was reported to carry speech intelligibly for miles. This water-borne application is reminiscent of the Russian harbour auxetophones mentioned just below.
|
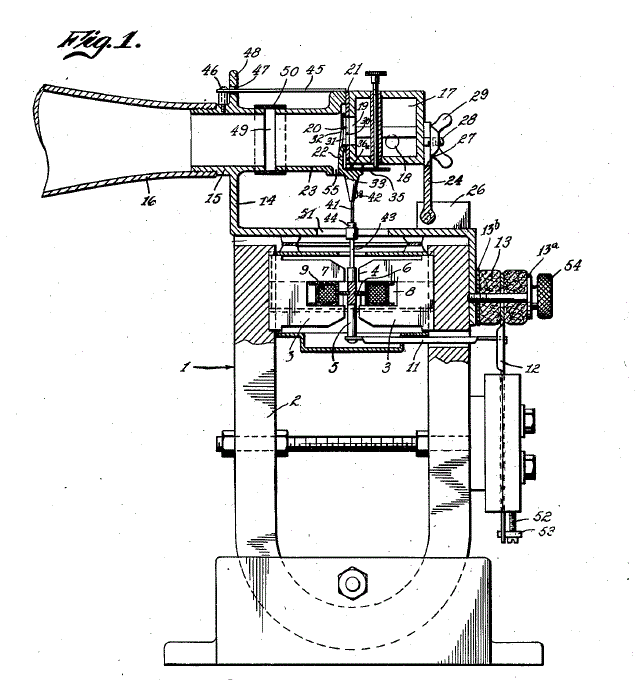 |
| Left: The Hetzel loudspeaker patent: 1933
There is a large U-shaped magnet labelled 1. The voice-coil windings 9 move the armature 5, which in turn moves a plate carrying a series of slots. This slides over another fixed slotted plate so that the slots coincide or other wise. I quote from the patent: "There should be one more of the slots 30 than the slots 31. This appears to be important and the movable grid should be adjusted so that its slots 31 are exactly midway between the slots 30."
It is unusual to find a phrase like "This appears to be important..." in a patent; claims are usually advanced with great confidence.
The patent does not seem to be any great advance on the valves of Short and Parsons.
|
THE HOOVENAIRE AIR COLUMN LOUDSPEAKER
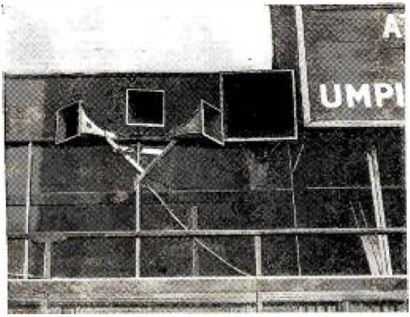 |
| Left: The Hoovenaire loudspeaker: 1931
The Hoovenaire system was devised by William C Eaves and C F Dilks. They used air at 20 psi, and 11 cu ft per minute was consumed.
This installation was at the Yankee stadium in New York. It was stated to have outperformed the previous system, while using less power. Whether the power for the compressor was taken into account is not known.
On one test the system was used in New York City to shout at people in New Jersey across the Hudson river. The electrical drive came from an amplifier "utilising two -50 type tubes, or about as much power as some people use in their radio sets in an ordinary sized living room. The people on the Jersey side heard every syllable perfectly." The "-50 type tube" mentioned is most likely a triode #50 which was common as an audio output tube in American radios from 1928-29. Read about it here; where it is dewscribed as a 25W tube. (valve in the UK) Thanks to Torbjörn Forsman from Sweden fot this information.
Source: Radio News for Jan 1931, p598
|
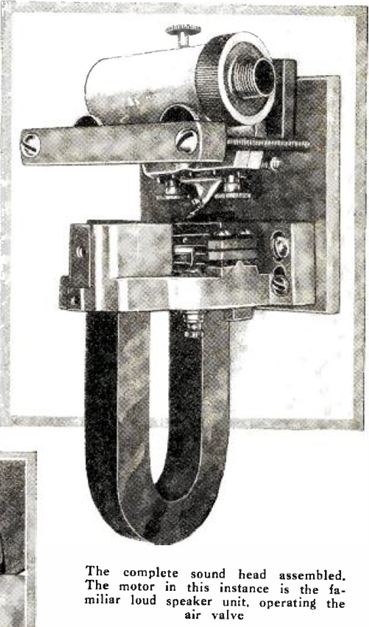 |
| Left: The Hoovenaire loudspeaker valve: 1931
The air valve was a flat plate with 16 vertical slits, with another light plate with 15 slits was placed against it; when the latter was moved by a coil and magnet as in a conventional loudspeaker, it controlled the air flow.
Source: as above.
|
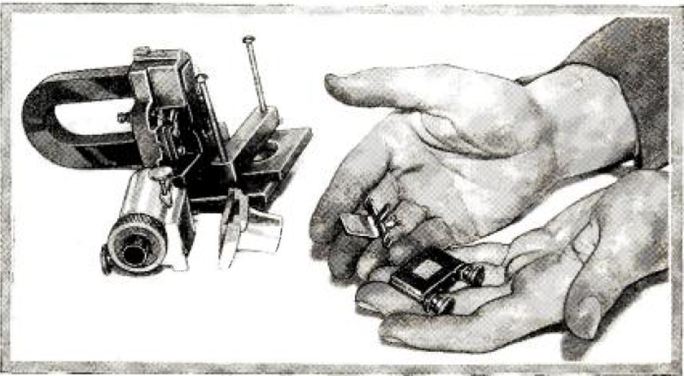 |
| Left: The Hoovenaire loudspeaker valve disassembled: 1931
This gives the scale of the parts of the valve. It appears to show the two slotted plates of the air valve, the fixed plate being on the right.
On the left is the electromagnetic unit. The small cylinder is the air passage in which the air valve is housed.
Source: as above.
|
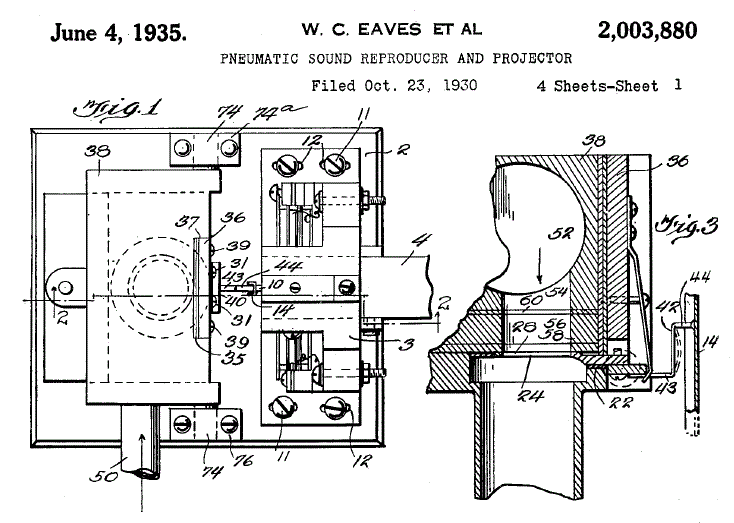 |
| Left: The Eaves & Dilks patent of 1935
Two Hoovenaire patents have been located so far, this one, and a later patent by Eaves only in Feb 1948.
4 is a horse-shoe permanent magnet. Between its poles is a coil which actuates the armature 10, visible in the centre of the drawing at left, which in turn moves the grid valve 24. Air enters through the pipe 50, is controlled by the grid valve, and then exits to the horn via the large pipe at the bottom of the drawing at right.
Source: US patent 2,003,880 of June 1935
|
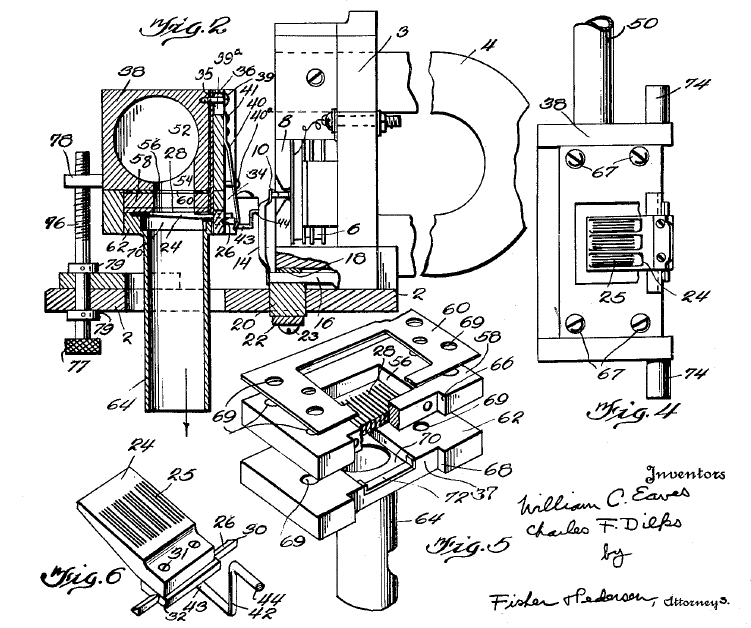 |
| Left: The Eaves & Dilks patent of 1935
Source: US patent 2,003,880 of June 1935
|
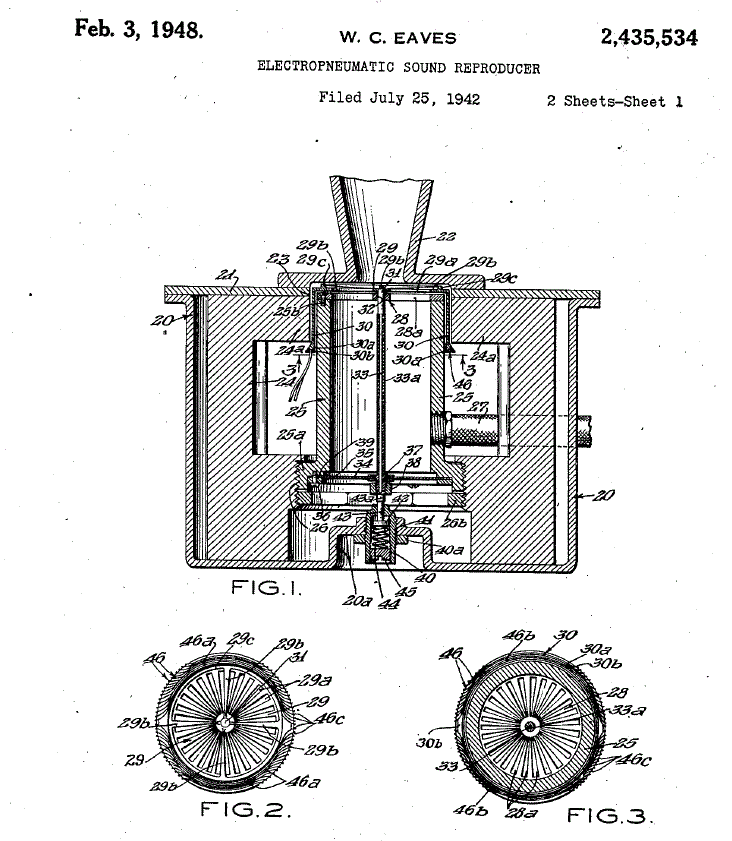 |
| Left: The Eaves patent of 1948
This shows a rather different valve design. Here the compressed air comes in through the narrow pipe to the right, and the outlet to the horn is at the top.
Source: US patent 2,435,534 of Feb 1948
|
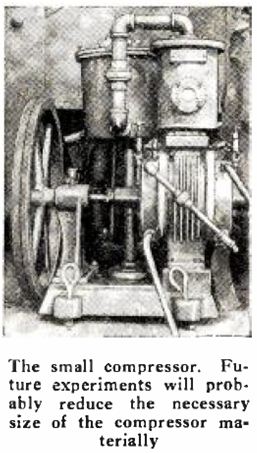 |
| Left: The Hoovenaire air compressor: 1931
This appears to be a water-cooled single-stage compressor; the vessel behind the cylinder is an air reservoir.
It is not obvious why the size of the compressor was a major issue, given the intended public-address applications.
Source: as above.
|
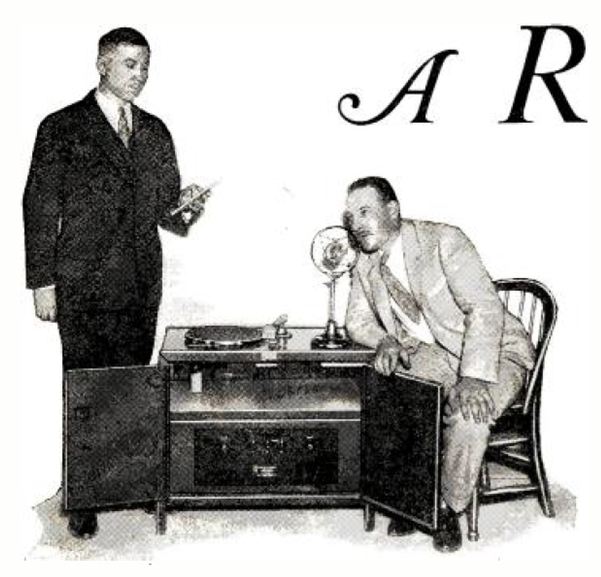 |
| Left: The Hoovenaire inventors William C Eaves (sitting) and C F Dilks: 1931
The console in the picture has a record deck and a microphone, so it might be the equipment used at the Yankee stadium.
Source: as above.
|
RUSSIAN AUXETOPHONES
According to The Great Soviet Encyclopedia (1979):
"Pneumatic loudspeakers were used in the 1930’s and 1940’s to transmit orders and information in large harbors, river ports, and other areas with a high noise level... Such loudspeakers produced an acoustic power of up to 2 kilowatts and reproduced audio-frequency oscillations with frequencies of up to 2.5–3.5 kilohertz, with high internal noise and substantial nonlinear distortion."
Two references are given:
Olson, H. F., and F. Massa. Prikladnaia akustika. Moscow, 1938.
Beranek, L. Akusticheskie izmereniia. Moscow, 1952.
The Museum Staff have not so far been able to find copies of either of them, though the latter book seems to be quite well known.
I know little about The Great Soviet Encyclopedia. I wouldn't trust it an inch on anything political, but there seems a good chance the non-glamorous technical stuff (eg not space flight) would be accurate.
No other information on this application has been found so far.
THE FLUIDICS APPROACH: A 1960s POSTSCRIPT.
Long after the machinery depicted here came fluidics, which is fluid control without mechanical parts, and there have been a few attempts in the past to use this technology for the direct amplification of sound. See The Fluidic Gramophone which appears to have got nowhere.
Is this an idea whose time has come? I suspect not, as reading a CD with jets of compressed air presents some interesting technological challenges...
AUXETOPHONE TECHNOLOGY TODAY.
Surprisingly, it's important. Very important, in its specialised field. We probably wouldn't have got to the moon without it. Compressed air modulated by valves is used to generate enormous sound levels in test chambers.
 |
| Left: Compressed-air noise generator.
The machine in the picture can generate a Sound Pressure Level of 165 dB from an air supply at 120 psi. The air is modulated by a servo-driven reciprocating poppet valve that sounds as though it is the direct descendant of Parson's comb-valve.
To put this in perspective, 130 dB SPL causes instant hearing damage. About the only thing in the world that generates such extreme levels as 165 dB is a rocket engine at close quarters- and that is exactly what these noise generators are used for- testing rockets and jet aircraft to make sure they can withstand the noise of their own engines.
For further details see: teamcorporation.com (external link)
|
Sometimes it is Rocket Science.
COMPRESSED-AIR LOUDSPEAKERS AT SOUTHAMPTON UNIVERSITY
Research on these devices continues. To get up to date on air-valves and the like, see Experiments on A Compressed-air Loudspeaker (1988) by Glendinning, Nelson, and Elliott at Southampton University. (NB, PDF download) Their experiments used a sliding-plate valve driven by an electrodynamic vibrator, and levels of at least 150 dB SPL were achieved. The authors note that such loudspeakers have been available since the 1950's,
and that units with acoustic power outputs from 4 kW to 20 kW are manufactured by Ling Electronics. Ling Electronics were bought out by Data Physics in 2009. It looks like they are still in the high intensity sound business.
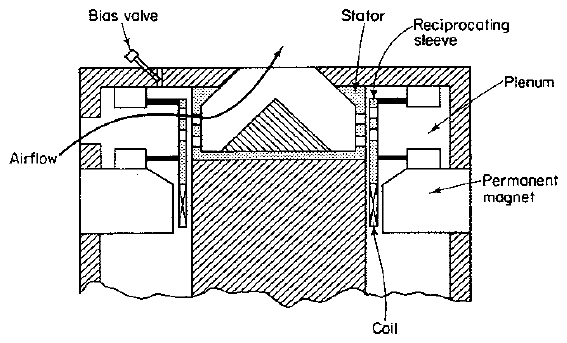 |
| Left: Cylindical compressed-air loudspeaker valve
According to Glendinning, Nelson, and Elliott, this is a typical contemporay design. There can be problems with wear of the cylindrical valve, and unbalanced axial forces due to air pressure imbalances. The bleed screw marked "bias valve" is one way of partly coping with the latter.
|
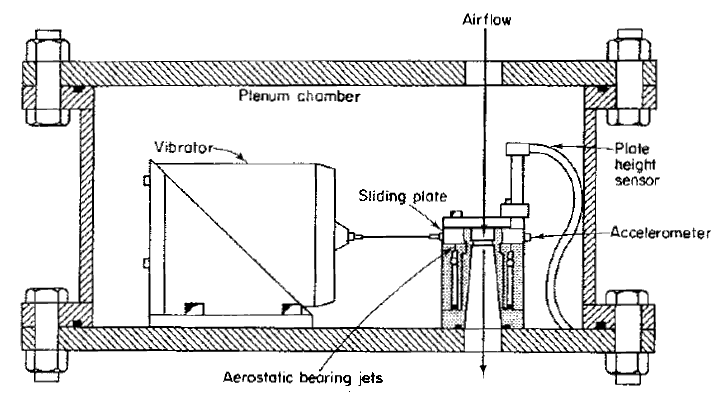 |
| Left: Sliding plate compressed-air loudspeaker valve
The experimental design used by Glendinning, Nelson, and Elliott. The sliding plate is supported on aerostatic thrust bearings to eliminate friction and allow operation without lubrication at high temperatures.
The authors state that a standard slot valve is inherently non-linear because the sideways pressure forces on the two plates vary with the degree of valve opening, They say that their design overcomes this problem but having read the whole paper I'm not sure how. According to their tests the second harmonic of the acoustic volume velocity is about 10% the level of the fundamental; higher harmonics are also significant. This was at 90 Hz.
The highest frequency used in the tests was 200 Hz.
|
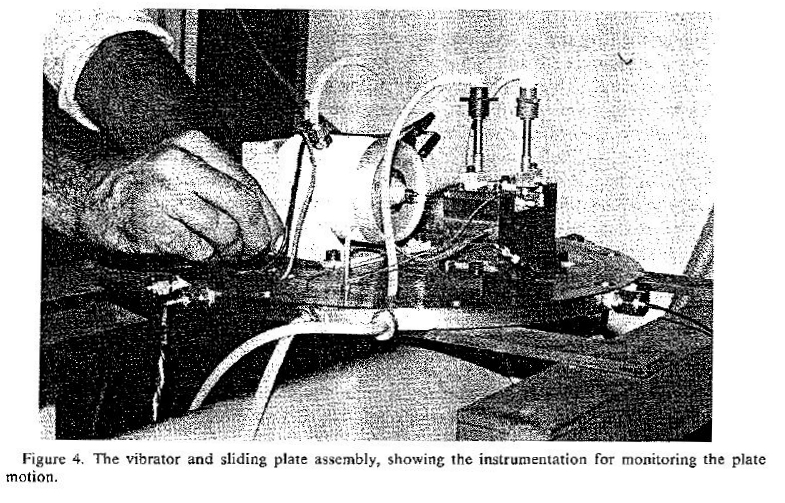 |
| Left: The experimantal assembly at Southampton
The electromechanical vibrator is the white cylinder in the centre. The sliding plate valve is the dark box to the right of it.
Source: Experiments on A Compressed-air Loudspeaker (1990) by Glendinning, Nelson, and Elliott: Journal of Sound and Vibration 138(3) pp479-491
|
Wyle Laboratories, of El Segundo, Calif., has developed a more compact solution, the WAS 3000. It is a powerful 30,000 Watt noise source capable of producing up to 165 dB of sound.